Trong môi trường nhà máy, các chi tiết máy móc sau một thời gian sẽ bị hao mòn như trục, gối đỡ, bạc đỡ,… Thậm chí chỉ sau vài tháng, các chi tiết này sẽ bị tổn hại đến mức độ nhất định và ảnh hưởng đến toàn bộ máy nói chung. Theo đó, để tránh tình trạng này, tại các nhà máy nhiệt điện, hóa chất, các kỹ sư đã phải áp dụng công nghệ phun phủ nhiệt để tạo ra lớp bảo vệ bề mặt nhằm kéo dài tuổi thọ hoặc phục hồi các thiết bị khi làm việc trong điều kiện có nhiệt độ, áp suất và các yếu tố gây mài mòn, ăn mòn khắc nghiệt.
Dẫu công nghệ phun phủ nhiệt có hiệu quả cao nhưng hiện nay, các lớp phủ nhiệt vẫn còn có nhiều điểm yếu ở cấu trúc khiến cho lớp bảo hộ không đạt được hiệu quả như mong muốn.
Cụ thể là vì các điểm yếu trên đã tạo nên các lỗ xốp khiến cho các tác nhân ăn mòn như nước biển có thể thâm nhập vào trong, gây ảnh hưởng nghiêm trọng đến khả năng bảo vệ chống ăn mòn cũng như khả năng chịu mài mòn của lớp phủ.
Để tìm ra câu trả lời nhằm bù đắp lỗ hổng nghiêm trọng này, nhà khoa học trên khắp thế giới đã nghiên cứu trong nhiều năm và đã đưa ra nhiều biện pháp khả quan như dùng nhiệt, laser, lắng đọng hóa học kim loại – chất hữu cơ, hay xử lý bằng phương pháp cơ học như mài, đánh bóng,…
Trong số các phương pháp này, TS. Nguyễn Văn Tuấn và các đồng nghiệp đã chú ý đến phương pháp thẩm thấu lớp phủ với các hợp chất có độ bền hóa học và độ bền mài mòn cao.
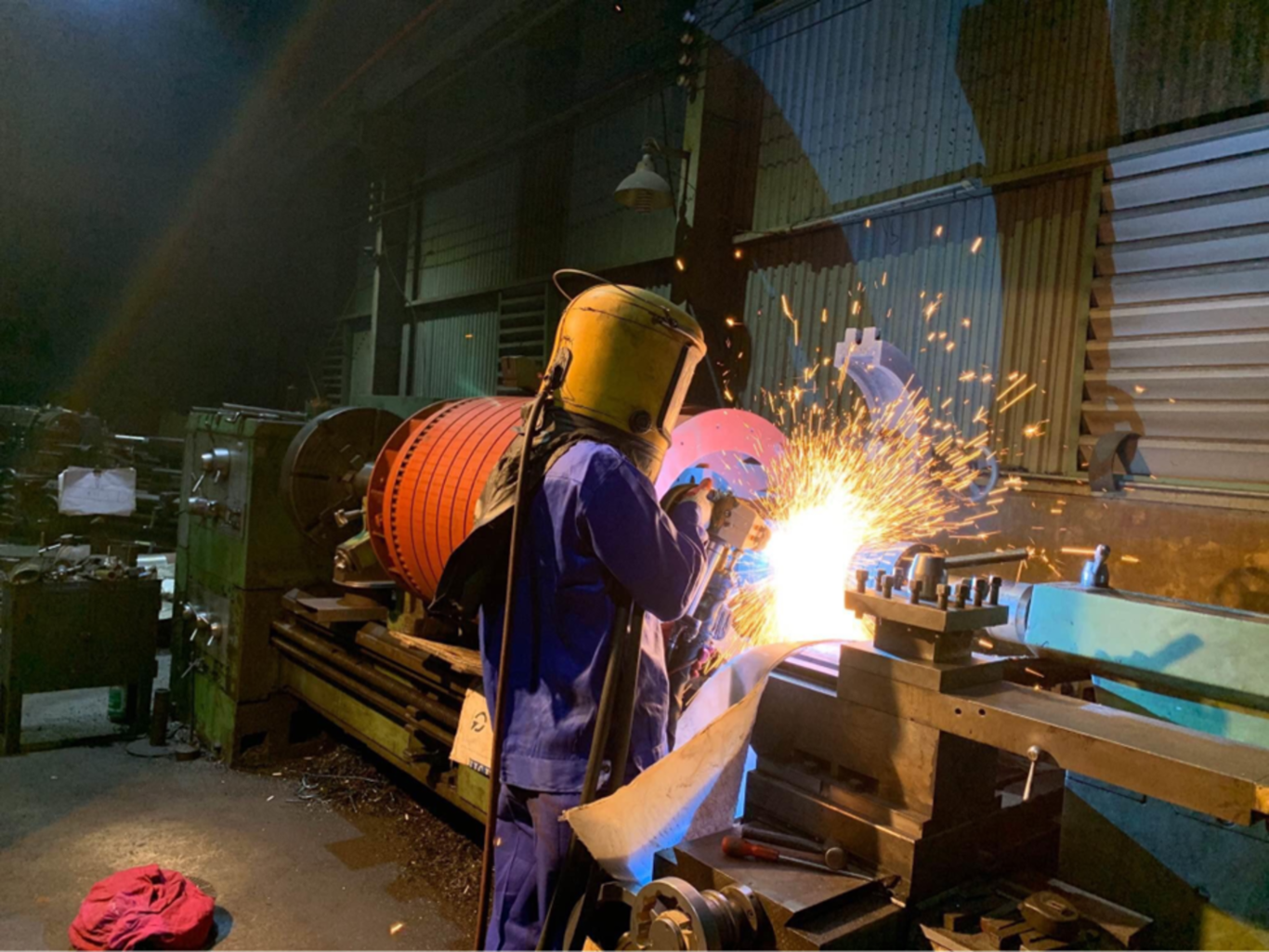
Tuy nhiên, dù tìm ra được hướng đi nhưng giữa vô vàn hợp chất, TS. Tuấn và cộng sự vẫn phải tìm ra loại hợp chất phù hợp nhất để đạt hiệu quả tối ưu cho phương pháp phun khử nhiệt.
Sau nhiều thử nghiệm, cuối cùng nhóm nghiên cứu đã nghĩ đến polytetrafloetylen (PTFE) – một vật liệu mà trạng thái hóa rắn của nó được dùng trong phanh xe đạp.
TS. Tuấn cho biết: “Đây là vật liệu có hệ số ma sát rất thấp (0,05 – 0,1), chỉ đứng sau kim cương nên có khả năng chịu mài mòn rất cao. Thêm vào đó, vật liệu này còn có thể chịu được hầu hết các loại hóa chất từ acid đến bazơ, cũng như chịu mức nhiệt lên đến 270°C, do đó sẽ không làm ảnh hưởng đến các tính chất vốn có của lớp phủ.”
Quy trình phun phủ nhiệt
Quy trình phun phủ nhiệt của TS. Nguyễn Văn Tuấn và các cộng sự được thực hiện như sau: Các hạt PTFE được nhóm sử dụng nước khử ion và chất trợ phân tán để đưa về kích thước từ 100 – 200 nm. Hàm lượng của PTFE phù hợp được nhóm xác định nằm ở khoảng 50-65% trọng lượng – mức hàm lượng có độ nhớt thích hợp để thẩm thấu.
Sau đó, hỗn hợp PTFE được đưa vào các bể rung siêu âm với tần số từ 20 – 50 kHZ để ngâm các chi tiết máy đã được phun phủ nhiệt trong khoảng 3-6 giờ. Cuối cùng, bề mặt chi tiết sau khi đã thẩm thấu PTFE sẽ được xử lý lần lượt ở các mức nhiệt 120°C, 170°C và 270°C rồi làm nguội trong buồng sấy.
Ngoài độ hiệu quả cao được chứng minh qua các thử nghiệm, phương pháp phun khử nhiệt của nhóm nghiên cứu cũng thể hiện rõ hiệu quả kinh tế khi có khả năng giảm từ 50-80% chi phí vận hành đối với các chi tiết máy làm việc trong các môi trường khắc nghiệt.
Giải pháp của nhóm nghiên cứu có thể được áp dụng được cho tất cả các loại lớp phun phủ nhiệt bề mặt trong lĩnh vực công nghiệp như lớp phủ kim loại, hợp kim, gốm, dù được chế tạo bằng các phương pháp phun nhiệt khác nhau như dùng khí cháy, hồ quang điện, plasma,…
Quy trình xử lý lớp phun phủ nhiệt bằng phương pháp thẩm thấu với PTFE trong điều kiện có rung siêu âm của nhóm TS. Nguyễn Văn Tuấn đã được Cục Sở hữu trí tuệ cấp bằng độc quyền sáng chế số 1-0031384 công bố ngày 25/03/2022.
(Theo Bài viết hợp tác giữa Cục Sở hữu trí tuệ và Báo Khoa học và Phát triển)